Plastics Manufacturing
Plastics Manufacturing Solutions
Many applications for plastic extrusion require repeatability and automation. Proportion-Air’s closed-loop systems can provide this through our pressure regulators, control valves and other custom solutions.
Direct applications include:
- The automation of blow mold machines during PET bottle molding applications
- Regulation of high pressure nitrogen in plastic bottom pre-forms
- Controlling high pressure in gas-assist injection molding
- Regulating pressure of nitrogen in high pressure leak tests
- Using air to maintain diameter and thickness of plastics during medical tubing extrusion
- Mixing of materials through the use of FCV flow control valve
- Control of pressure during plastic painting applications
- The control of temperature in a plastic injection molding machine
- Thermoforming through the use of electronic vacuum regulator assemblies
The manufacturing of any kind of tubing, from PVC pipes to hospital tubing, requires precision in its extrusion. Plastic pellets are heated and forced through a die that provides the shape (thickness and diameter) of the product. At this point, the hot plastic is limp and flexible and precise pressure controls are critical.
The extruded tube travels through a cooling chamber where vacuum is used to maintain the tube’s shape as it hardens. Precise air pressure is fed through the inside of the tube to maintain a consistent product.
On the inside, water cools the material to a specific hardness in the cooling chamber; on the outside, a vacuum helps maintain the correct outer diameter. Both require pressure and both are controlled efficiently and predictably with our closed loop systems.
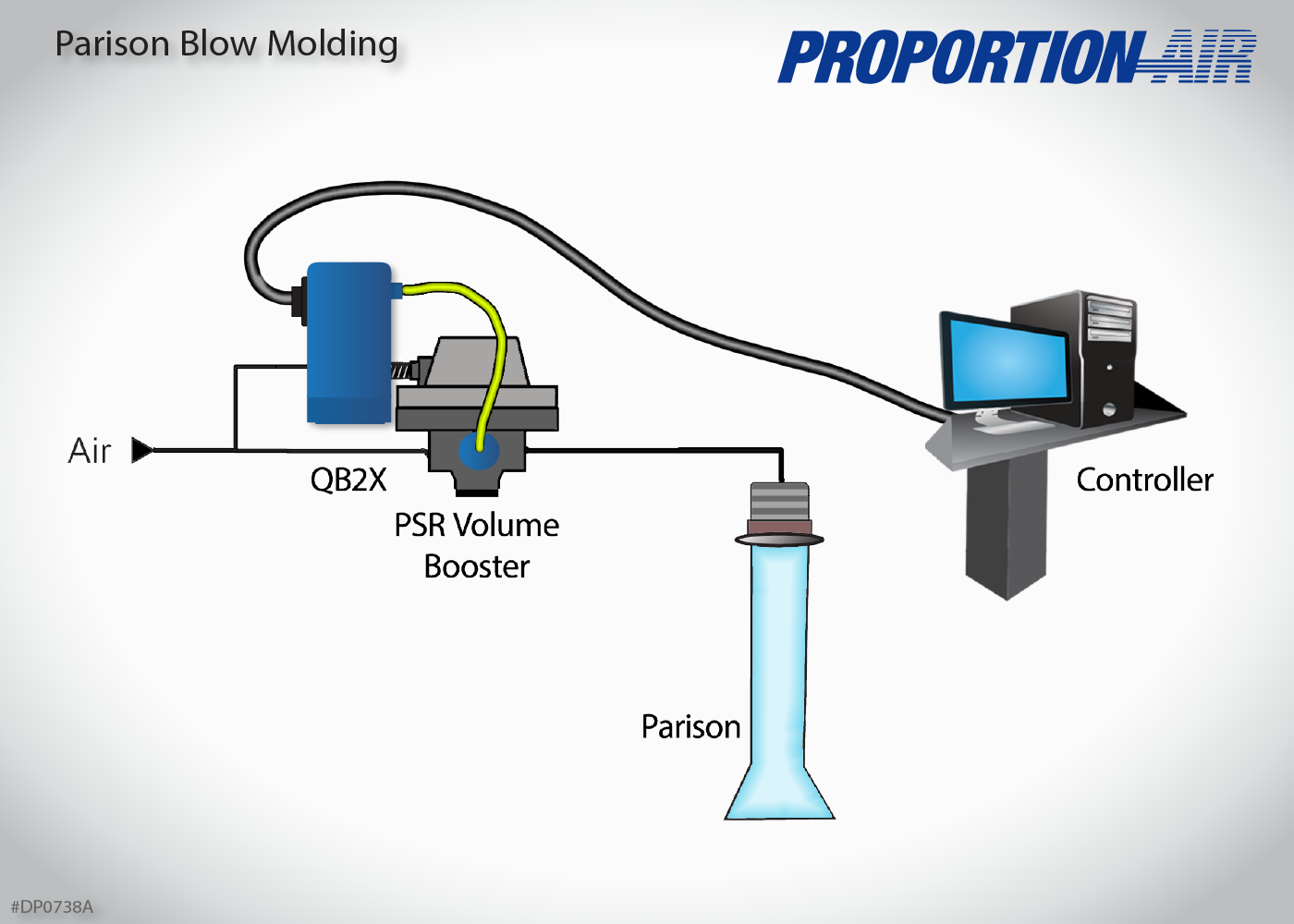