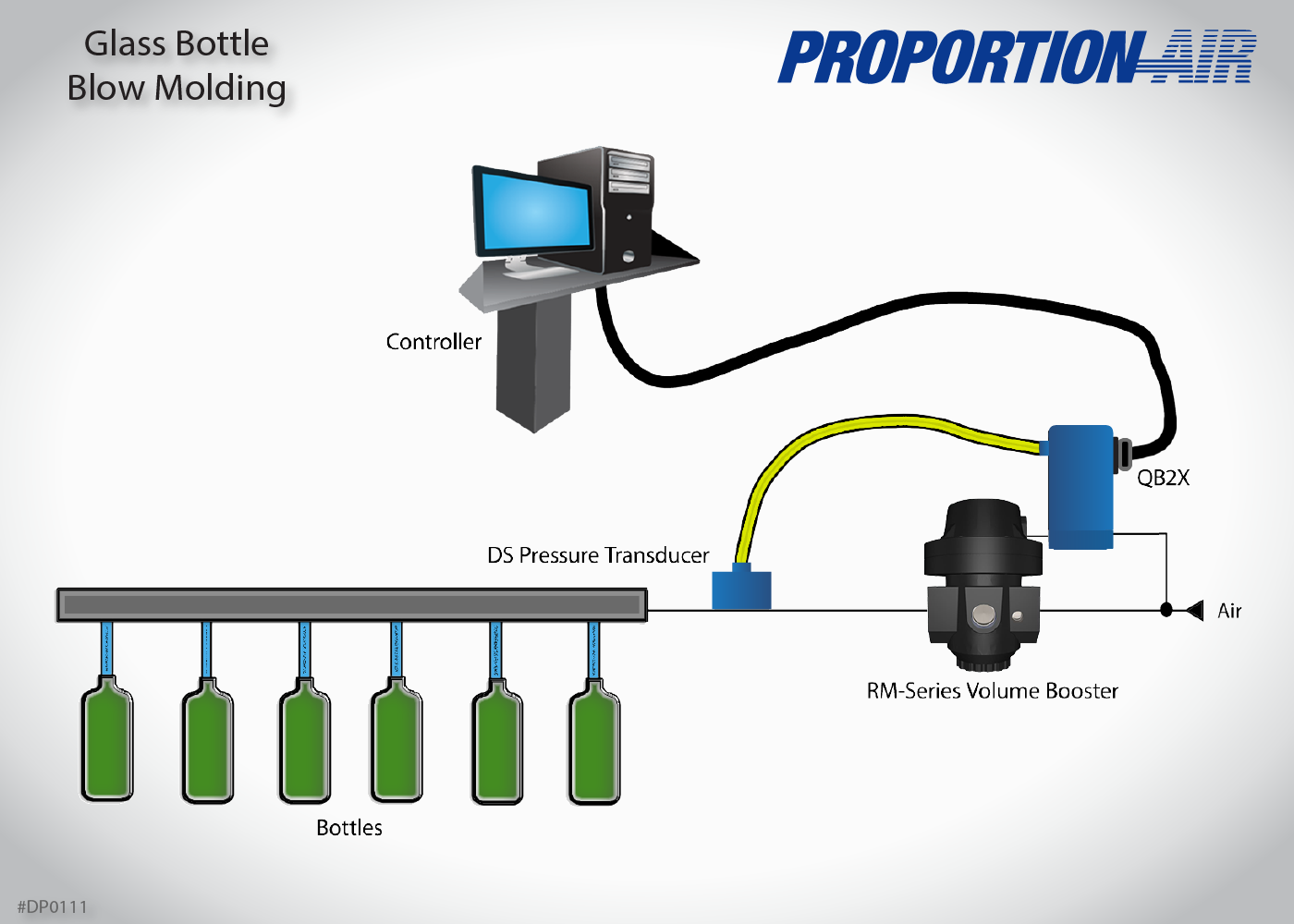
This sketch shows a QB2 piloting a 2-inch ported volume booster in a glass bottle blow molding application. Pressure can be changed on the fly by adjusting the command signal from a computer or controller. The QB2 volume booster and DS assembly is accurate to ±0.2% and repeatable to ±0.02% of full scale calibration.
Most glass bottles are manufactured via the “press & blow” method. This method heats the glass to around 1200 degrees Celsius or until the glass enters its “plastic stage.” At this point, the molten glass takes on a cylindrical shape and it is called a gob. This gob is then pressed into a mold, to whatever the final shape will be. Pressure is then used to spread the gob throughout the mold.
Many bottles can be created at the same time using this process. The pressure control must be fast responding, accurate and repeatable to ensure consistent glass bottles blow molding.
Products used in this application:
-
QBX Industrial Electronic Pressure Regulator
$576.00 Select options This product has multiple variants. The options may be chosen on the product page -
DST High Pressure Transducer
Read more -
RM Pilot-Operated Regulator
Read more