Compressed air is nearly ubiquitous in factories. It’s part of the power behind everything from CNC machines to cylinders to hand-held tools. The inescapable nature of compressed air can provide a false sense of security around its safety.
A review of the US Occupational Safety and Health Administration’s (OSHA’s) accident search website shows only a small portion of major accidents involved air pressure, compressed air or similar pneumatic themes. However, in 2023, all of the more than 20 accidents related to those terms were fatalities. Many compressed air injuries may be going unreported or unrecognized.
One area that offers easy ways for improved safety is using compressed air hoses properly. Whether for cleaning or providing compressed air to a device or system, these hoses can simultaneously be a powerful tool and a hazard.
What Not to Clean
Cleaning is one of the most common uses for compressed air, whether workers are blowing debris from machines, products or even themselves. Compressed air is safe and effective at the right pressure for some of these tasks, but not all.
While it may be a common practice, using compressed air to blow debris from a person’s body or their clothing is more dangerous than many suspect. Compressed air can be forceful enough to cause skin lacerations. Pushing air inside those cuts or an existing laceration can lead to swelling and pain. That air can also carry contaminants that can lead to infection. In the most extreme cases, air entering the bloodstream can result in an embolism. Embolisms from compressed air are rare but can result in a coma, paralysis or even death.
Pointing a hose toward someone’s head can injure eyes or ears, and travel to internal organs. Regularly using compressed air close to the ear is likely to cause permanent hearing damage without proper protection. Pressurized air that is 40 psi or greater can cause an eardrum to rupture if it is four inches or closer to the head. A mere 12 psi can blow an eyeball from its socket. Compressed air that enters through the mouth can get to the lungs.
The head isn’t the only access for compressed air to enter the body. Air blown at the navel can even enter the intestines.
Cleaning Workspaces and Products
Workspaces and physical products can be cleaned with compressed air as long as proper precautions are taken. Compressed air must be limited to less than 30 psi to execute these types of cleaning. This is the guideline OSHA publishes for using hand and portable power tools (see OSHA 29 CFR Part 1910.242(b) for additional details). The pressure can be limited at the source or by using a regulator.
Compressed air does not have to come into direct contact with skin to cause injury. When cleaning manufactured components or products, debris like dirt, wood dust or paint can become airborne, hurling at exposed skin and causing significant pain. Cleaning floors with compressed air can kick up debris that when inhaled can cause respiratory issues.
To alleviate these risks, perform compressed air cleaning with personal protective equipment, air regulation, and chip guards. Effective chip guarding methods or equipment will reduce the chance that a chip or particle of any size is blown into the eyes or skin of the operator or other workers in the area.
Safety with Tools
When compressed air is powering a tool or system, the pressure in the hose isn’t the only threat. Hoses can present a tripping hazard.
Hoses shouldn’t be put in high traffic areas where they can be stepped on or driven over. Ideally hoses should be on retractable reels and stored overhead as close to the workspace as possible. This keeps them off the ground and easily accessible for workers. Hoses should be retracted when not in use.
Workers should always check connections before turning on air, ensuring they’re secure. Qualified personnel should choose appropriate couplings for the work at hand.
If a hose is cut, bursts or otherwise gets out of control, workers should be instructed to get out of the way and shut off the air supply at the source.
Protecting Against Compressed Air Hose Risks
To properly protect from these risks, creating a culture that values safety is a priority.
Employees should use goggles or face shields to protect their eyes and ear protection like earmuffs or ear plugs. This lowers the likelihood of a facial or ear injury.
Hose maintenance and preventive care can make a big difference. Compressed air hoses should be checked regularly for leaks, frays or damage. Replace damaged or deteriorating hoses immediately.
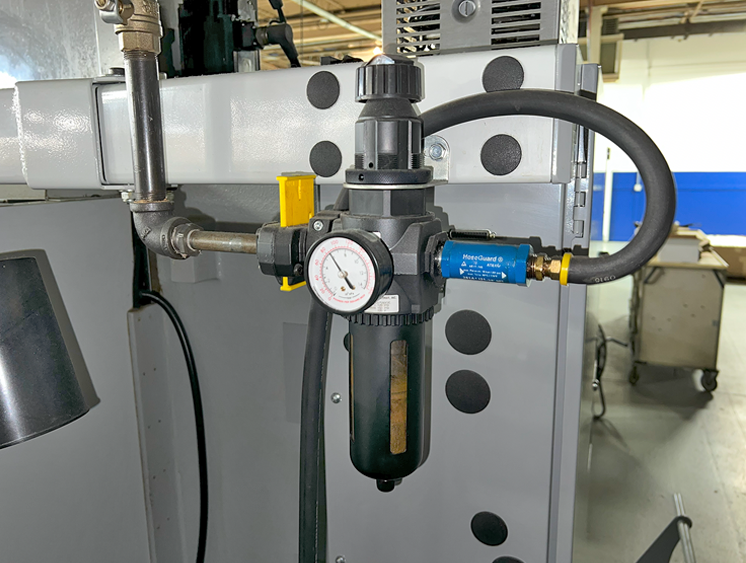
In addition to those broad guidelines, several options exist for protecting personnel and equipment from compressed air hose accidents. Hose whipping can happen when a hose is damaged or bursts. One way to prevent hoses from whipping is to use an air fuse like the HoseGuard. An air fuse prevents hose whiplash by stopping compressed air when it exceeds a pre-set flow.
Another way to protect personnel and compressed air systems or tools is to install a regulator between the hose and the tool. Small, in-line regulators like the CartReg or SaveAir can be put in the supply line before the tool receiving air. The regulator limits the pressure going to the device, reducing the risk of overpressurization. The CartReg is also available in a 29 PSI option, making it an ideal regulator to limit the pressure on hoses used for cleaning.
Safe and Cost-Effective
Not only does using air fuses and regulators create a safer environment, but it can also create a more cost-effective one. Compressed air is an expense that many manufacturers accept without much thought, but it can be alleviated. For some tools or systems, pressure and flow at the withdrawal point is higher than those specified by the manufacturer to achieve the desired function. By limiting the pressure to only the required outlet pressure with a product like the SaveAir miniature regulator, users can avoid this dynamic pressure waste.
By employing safety protocols while properly maintaining and regulating compressed air hoses, manufacturers can create a safety-first environment that limits accidents and reduces costs.