Before taking to the skies in a plane or a space shuttle, any number of tests must be done to ensure a safe experience for the people and equipment involved. Providing realistic aerospace simulations of flight conditions is an essential aspect of both aircraft design and training.
Proportion-Air offers solutions for accurate pressure and flow control in many aerospace simulations, whether for military purposes, commercial air travel or exploring the far corners of the universe.
G-Suit Simulation
When a human body is subjected to high levels of acceleration force, commonly known as g-force, blood may not circulate properly. In these cases, it often accumulates in the legs and abdomen. This can cause an aviator or astronaut to lose consciousness. A g-suit is a flight suit that applies pressure to the legs and abdomen. Applying pressure in those areas keep blood flowing throughout the body, ensuring that the brain isn’t starved.
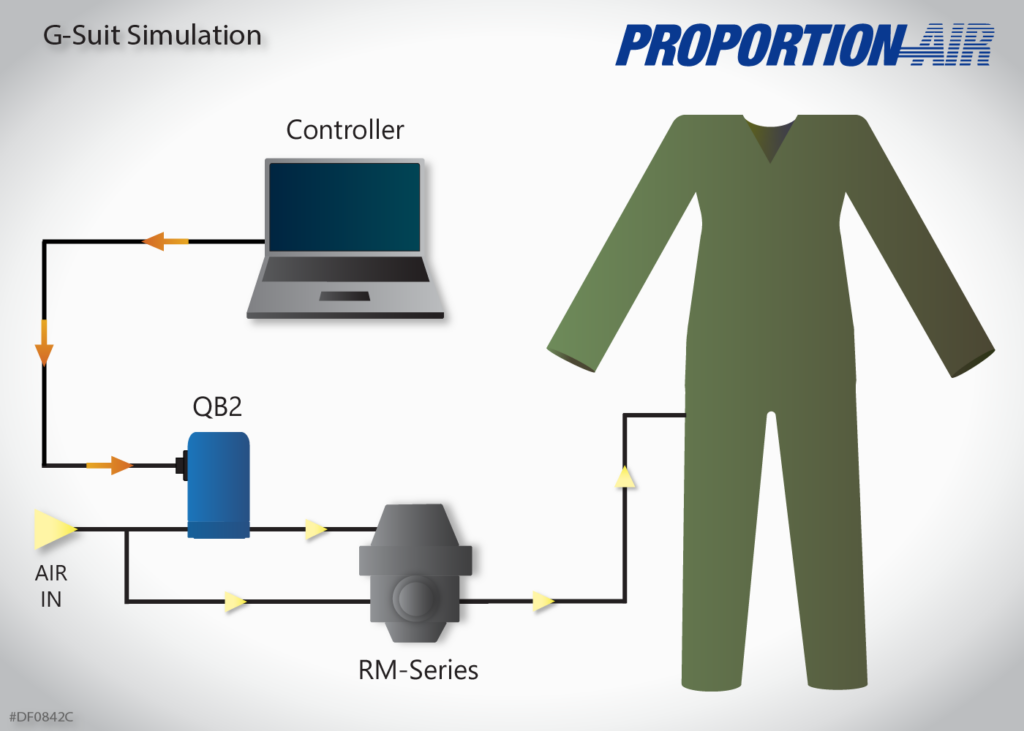
Flight Simulator Controls
Creating the experience of sitting behind an aircraft’s controls requires more than just the panel itself. The potential changes in the craft’s internal and external environments must be replicated in a way that offers a designer or pilot the opportunity to learn about configurations or reactions necessary for a safe flight.
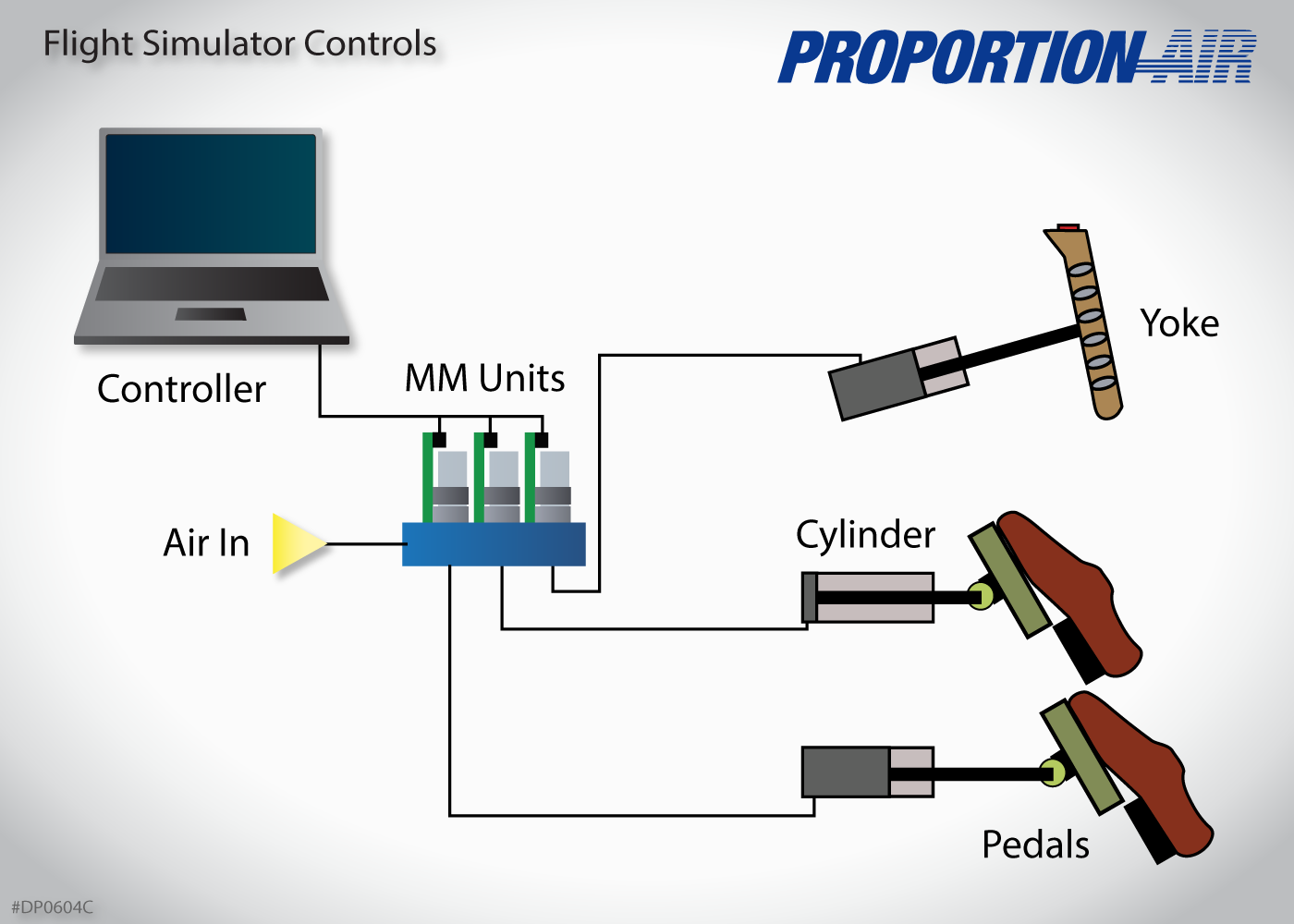
Flight Simulator Seat Forces
Military flight simulators must include the simulation of the flight suit, belt and air bladders like those used on the actual aircraft. Pressure requirements on flight simulator seat forces are sometimes as low as 1 psig full scale, yet air must be added and vented quickly to respond as changes are required.
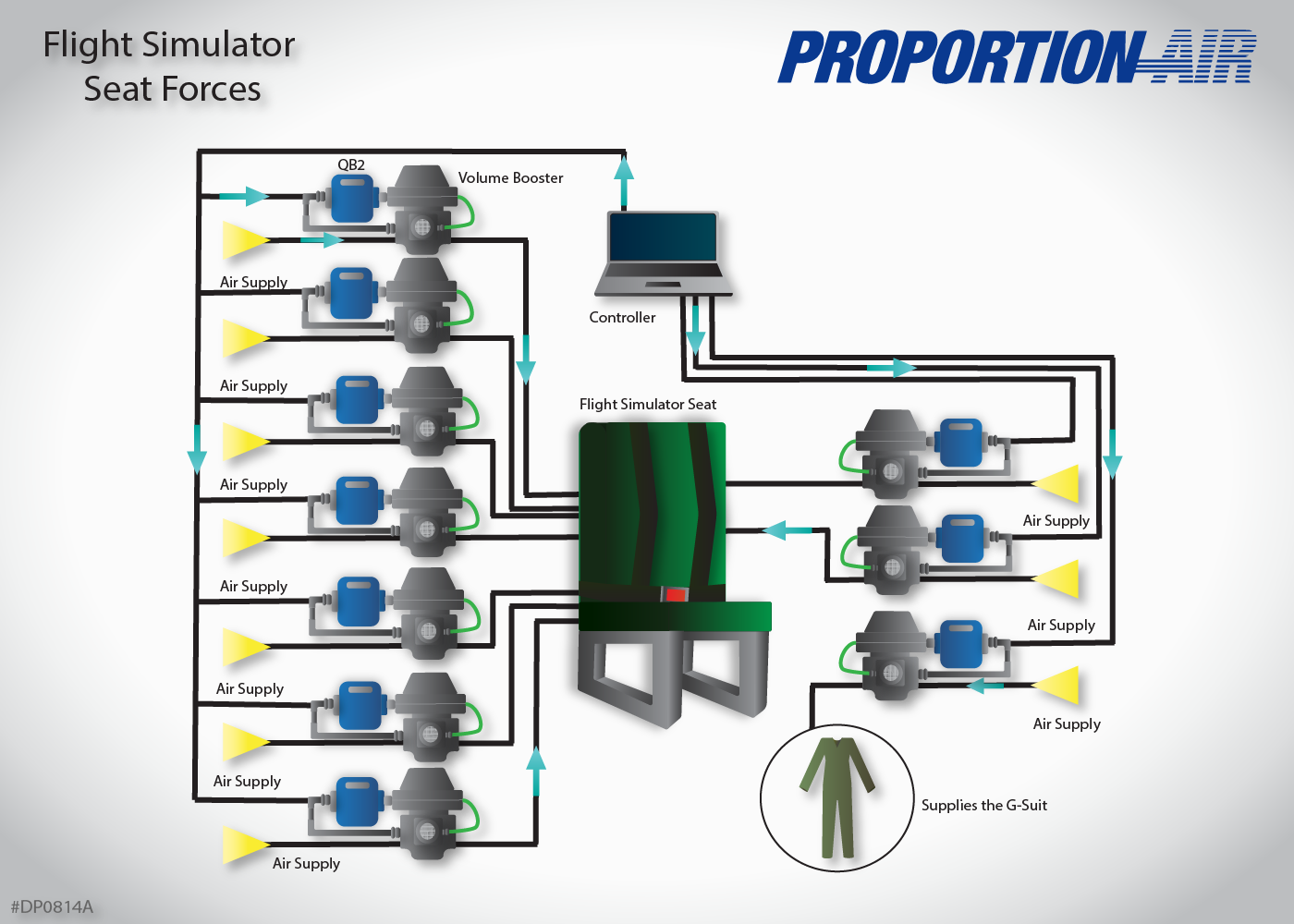
Altitude Simulation
Often, aircraft components must be tested at the different altitudes that they will experience in service. This testing ensures that the components can withstand the conditions they will be subjected to while in flight.
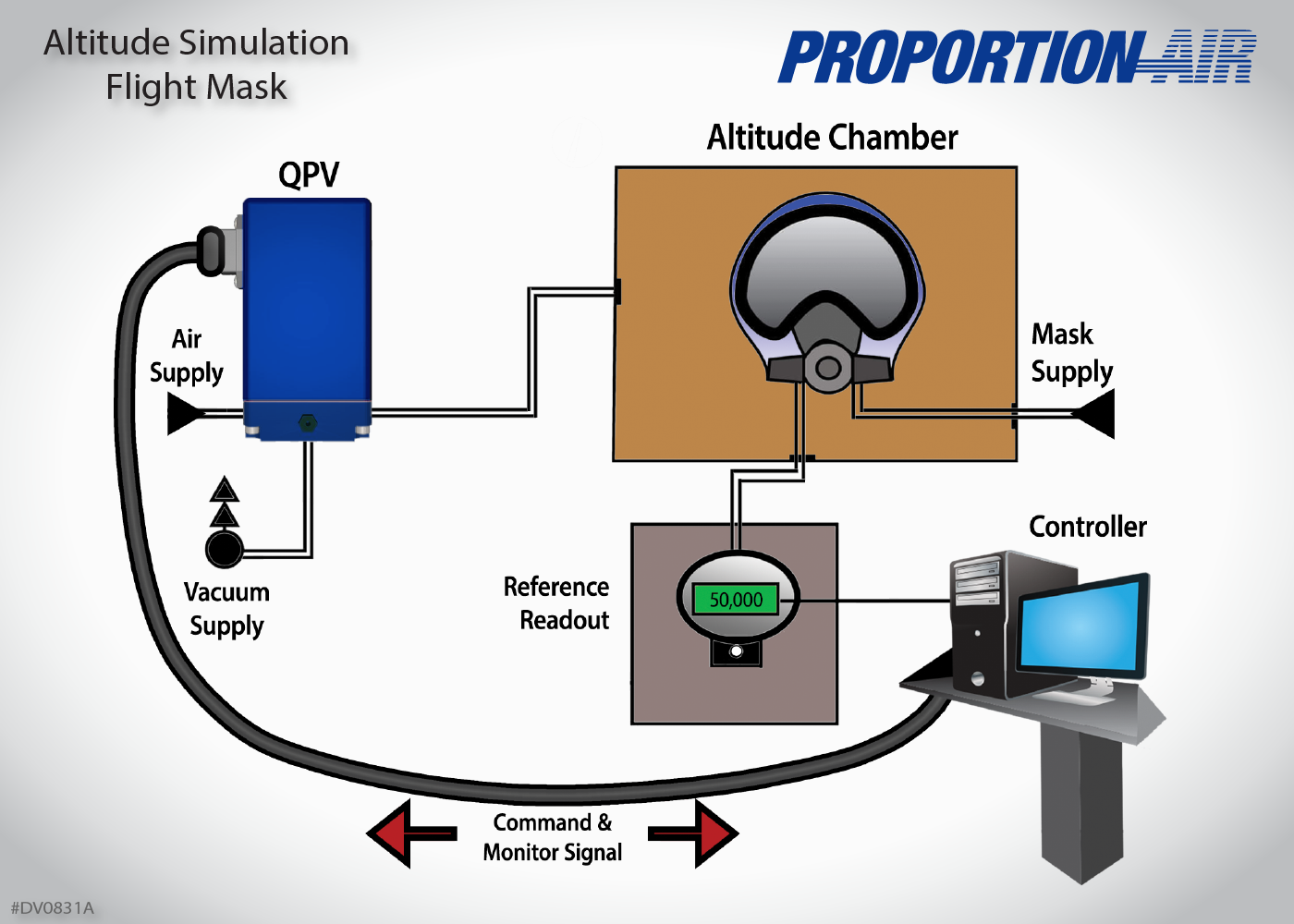
Fuselage Stress Test
In aircraft manufacturing, components must be tested for stress they would encounter during flight. The fuselage stress test aims to simulate constantly changing atmospheric conditions. Designers then review the effects of the changes on the main body of the aircraft. The challenge in this type of testing is the large volume that must be pressurized and exhausted as quickly as possible.
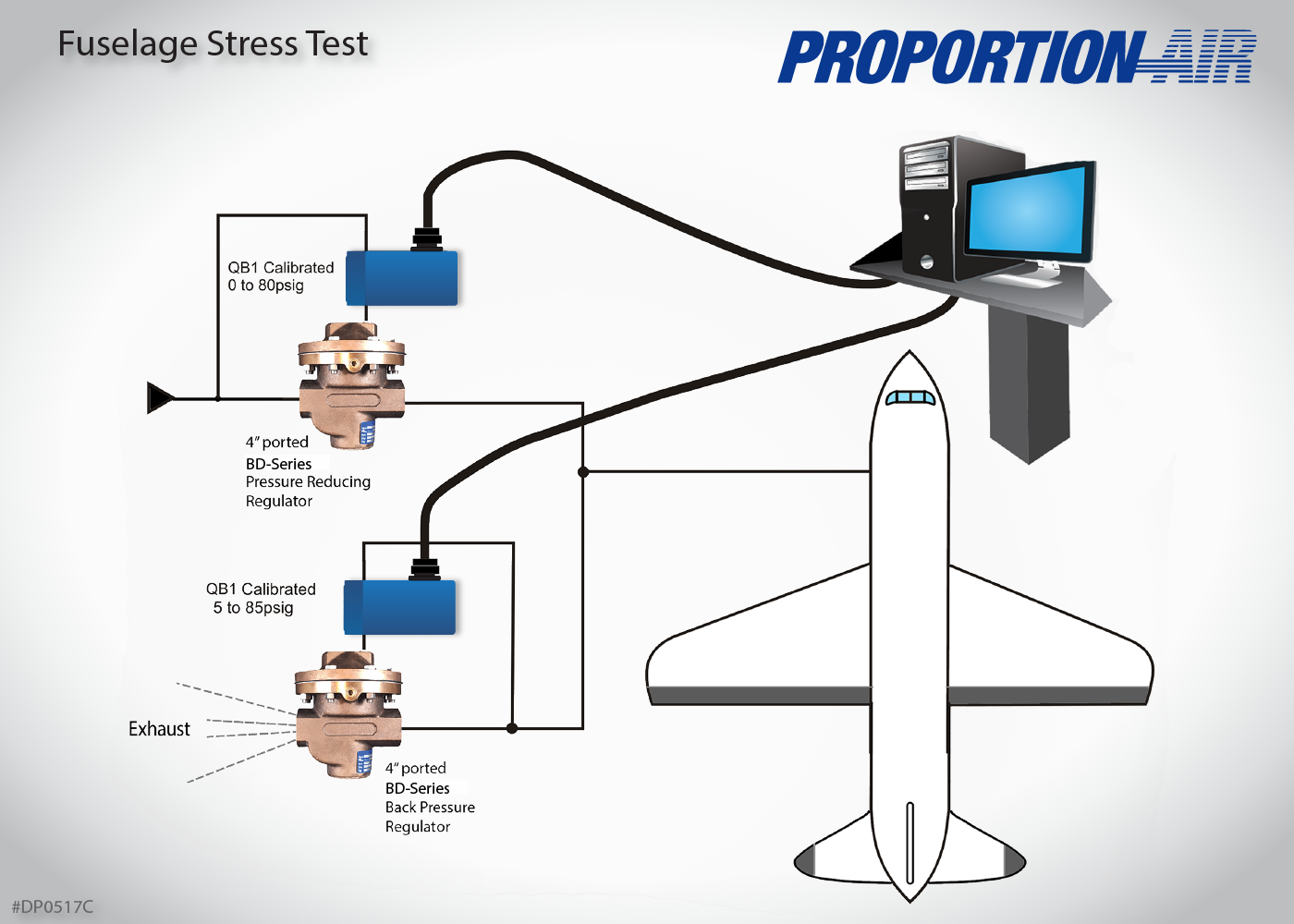
Fuselage Fatigue Testing
Aircraft undergo a multitude of conditions in flight that can cause structural stress on the fuselage, the main body of the aircraft. Fatigue fractures come from repeated stress that damages the fuselage but doesn’t cause immediate failure. These fractures continue to grow as stress is applied. This reduces the integrity of the body and the safe life of the plane.
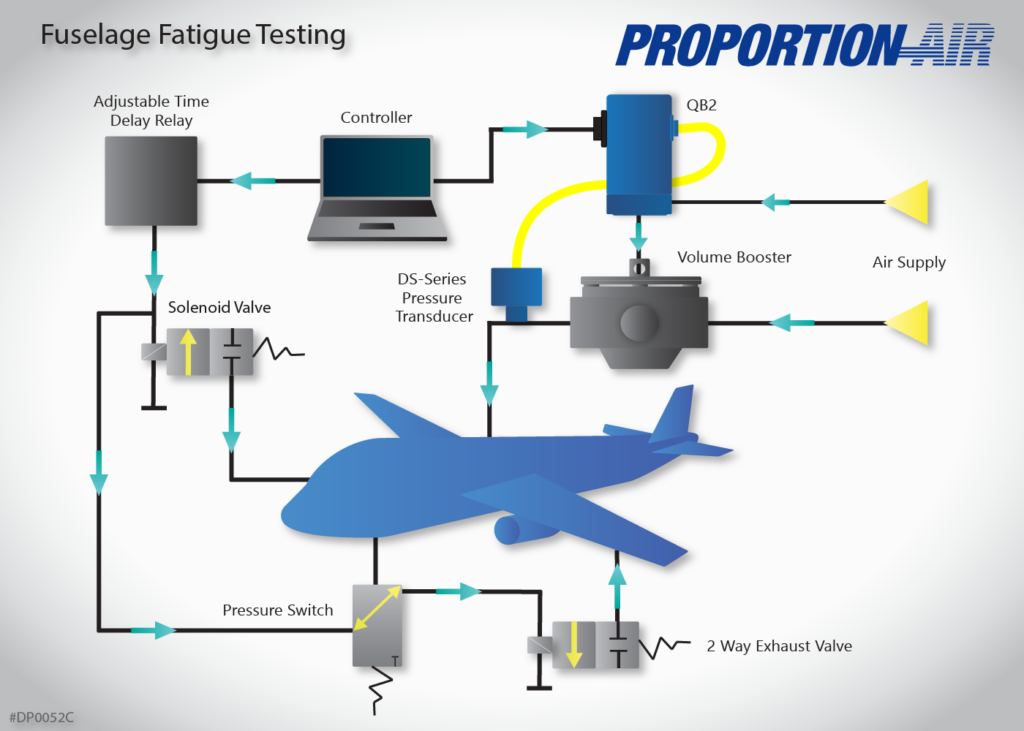
Proportion-Air Delivers for Aerospace Simulations
Proportion-Air products are a great fit for nearly any aerospace simulation that requires pressure regulation. Accurate, repeatable, customizable proportional pressure control can ensure that the most demanding tests are accomplished with certainty.