Electronic Pressure Regulators
Proportion-Air is the universal leader for proportional electro-pneumatic pressure regulators. We offer the most accurate, repeatable, customizable products on the market today.
Our expertise in electro-pneumatic regulators is in vacuum, low pressure and high pressure control applications that require excellent repeatability. If you do not see what you are looking for, please contact us. Our customization options are nearly unlimited.
Have additional questions? Visit our FAQs below to look for your question.
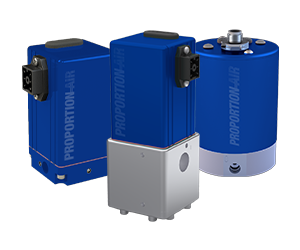
High Pressure Valves
1:1 direct control up to 1,000 psi; ratio regulator assemblies for even higher valuesLearn More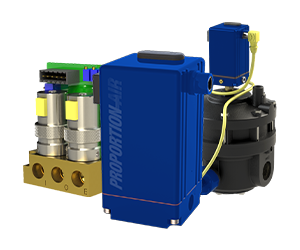
Low Pressure Valves
175 psi or lower; down to 0-2" of water column full scale for sensitive applicationsLearn More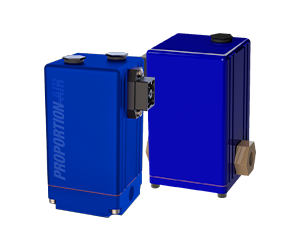
Hazardous Location Valves
FM-approved nonincendive or intrinsically safe regulators for classified hazardous areasLearn MoreFrequently Asked Questions
Electronic pressure regulators regulate pressure in a system in response to a network, voltage, or current command signal. The output pressure is proportional to the command signal. Electronic pressure regulators use solenoid or proportional valves, pressure sensors, and electronic controls to achieve precise pressure control.
Electronic pressure regulators offer superior precision and faster response times compared to mechanical regulators. They are not affected by, and can correct for the mechanical issues that cause droop, hysteresis, or other mechanical issues in a mechanical regulator. They excel in maintaining stable pressure, especially under fluctuating supply and process conditions.
Yes, they can integrate with various automation systems, enabling remote control and monitoring through various analog voltage, current, and digital interfaces such as RS-232, RS-485, or Ethernet.
Electronic pressure regulators are generally more expensive at purchase than mechanical pressure regulators due to their advanced technology. However, the enhanced control and efficiency they provide can justify the higher cost.
Some of the advantages include, but are not limited to, superior accuracy and repeatability in pressure control, faster response to pressure changes, enhanced controllability via digital settings and feedback loops, data logging for process optimization, and potential for remote control and automation integration.
Factors to consider are desired pressure range, flow rate, fluid type, operating environment, and control requirements. For better assistance, our team is always available to lend a helping hand. Please contact us!
Electronic pressure regulators control system pressure by comparing the command (desired pressure) with the feedback (actual pressure sensed by a pressure sensor) and operating an inlet valve to increase pressure or opening an exhaust valve to decrease pressure, to achieve the desired pressure.
*We recommend reading the manufacturer’s manual for specific instructions*
Electronic pressure regulators are often remotely controlled, so a local means of making the regulator safe for maintenance may not be available. Therefore any maintenance requires proper lockout and tagout of the pressure source, power source, and command source to prevent inadvertent operation during maintenance.
Loss of electrical power or loss of control signals to an electronic regulator may place the system in an unsafe condition. This should be kept in mind when designing the system.
Regularly inspect for clogs, leaks, and wear; when repair kits are available, replace components like O-rings and seals as needed; keep components clean, especially in systems handling particulate matter.
The regulator should be rated for the maximum possible supply pressure that can be delivered to the system.
Static applications generally are not affected as much by inlet pressure fluctuations as applications under flow. A pressure regulator (electronic or mechanical) whose output is at setpoint has its valve(s) closed. A change in inlet pressure has minimal effect. For a regulator under flow or filling a vessel, a change in inlet pressure changes the differential pressure across the regulator valve and will affect the flow rate through the regulator. An electronic pressure regulator would detect this change in the feedback and adjust the regulator’s valve accordingly to maintain setpoint.