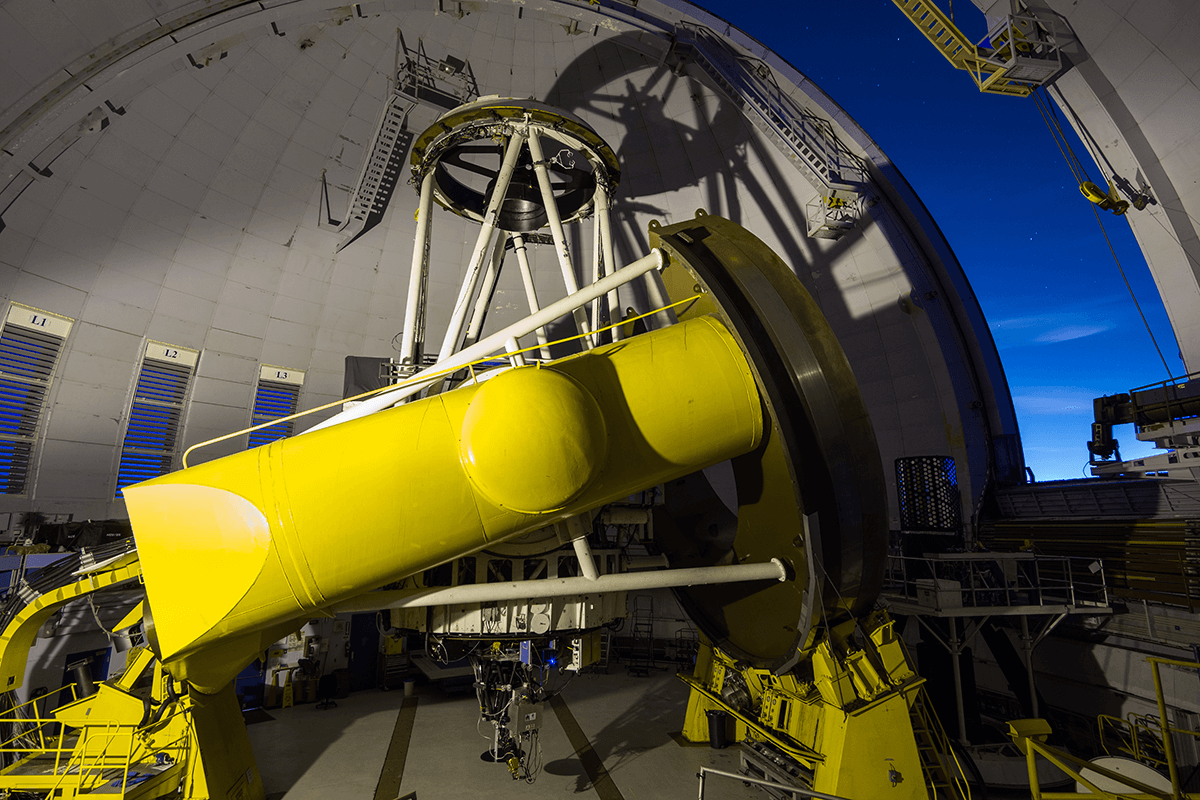
Background
The Canada-France-Hawaii (CFH) observatory hosts a world-class, 3.6-meter optical/infrared telescope. The observatory is located at the summit of Mauna Kea, a 4200-meter, dormant volcano located on the island of Hawaii. The CFH Telescope became operational in 1979. The mission of CFHT is to provide its user community with a versatile and state-of-the-art astronomical observing facility that is well-matched to the scientific goals of that community and fully utilizes the potential of the Maunakea site.
Primary Mirror Cosine Regulator Upgrade Needed
The telescope’s primary mirror is positioned on a set of pneumatic puck assemblies and three hardpoints. This maintains the mirror figure through the varying gravity vector by modulating the pressure that follows a cosine curve from zenith to horizon. Twenty-four pneumatic puck assemblies are placed around the mirror cell in two concentric circles, with fifteen pads forming the outside ring and nine on the inner. Load cells mounted on the hardpoints monitor the pneumatic support performance.
The original PM cosine regulator was a passive, mechanically based, open loop system, using mass and gravity to regulate the pressures driving the inner and outer rings of pneumatic mirror pucks of the support system. It has been very reliable over the past four-plus decades, however the mechanical regulator required constant air bleed to maintain the pressures. This resulted in a high air compressor duty cycle, which meant excessive electrical costs and air compressor usage.
The following observations of the existing system were noted:
- Incoming pressure to each regulator needs to be supplied by at least 0.0353 CFPS at 72 psi. That is 3049 cu-ft @ 72 psi/day/regulator.
- Pressure to each controller should be regulated to 35 psi +/- 2.85 psi.
- Controllers (regulators) should be aligned in two planes to within 2 arc-min.
- An alignment error of 3 minutes will cause a system error of 0.05% (0.005 psi) at a zenith angle of 90 degrees.
- Each of the 9 inner pads provide 1086 lbf at zenith. Each 15 outer pads provide 1034 lbf at zenith. Total of 25,284 lbs or 12.64 tons.
- Total load for the 9 inner pads, 15 outer pads, and 3 defining points should be 28,433 lbs.
- The system cost $65,789 in 1974 dollars, equivalent to around $400,000 today.
Design Objectives
In addition to meeting the necessary specifications for fault tolerances and fail-safes to reduce repair time in the case of damage, the objectives for the new regulator upgrade included:
High level of reliability
- Minimizing component count
- Using altitude-rated components when possible
- Minimizing the use of electrolytic capacitors
- Prevent control from faulty Raspberry Pi
- Using automotive-qualified parts wherever possible
- Use low-temperature dependent parts
Achieve a high level of maintainability
- Having tested spares on-hand
- Minimizing custom parts
- MIL-SPEC bulkhead connectors to the outside world
- Using legacy CFHT components where possible
- Having online parameter tuning
Proportion-Air Provides an Effective Pneumatic Solution
A new closed-loop system was designed to replace the old system. The new approach uses a microprocessor to control electronic pressure regulators and pressure sensors to provide feedback. This system does not require constant air bleed.
The new system was installed and tested extensively before being released for operations. It was calibrated and tuned to match the performance of the previously existing cosine regulator. Since the mirror support system is critical to image quality and damage to the mirror pucks could incur many man-hours of work, the new system was designed with multiple redundant features that allow for either false-safe or fault-tolerant, depending on the failure mode.
- Components were chosen to ensure high reliability and safety
- Circuit board was designed with hardware limitations that will intentionally prevent damage
- Programming philosophies were adopted from the space industry to ensure robust, standalone operation
- Proven command lockout scheme and control philosophies ensure safe command and setting of the new system gains
- By design, the system prevents the pneumatic pads from over-pressurizing
Substantial Cost Savings and Improved Accuracy
The original system cost was around $65,000, which today translates to roughly $400,000, including non-recurring engineering (NRE) costs. The pneumatic replacement system, including the necessary regulators, was only $5,000, thanks to its simplicity and not having to start from scratch. While NRE costs for the new system have yet to be determined, the savings with the new system are sure to remain substantial.
The customer reports that while the previous system performed well, it was fairly inaccurate. It also used a mechanical regulator with a constant air bleed. The new system, using Proportion-Air regulators, is much more accurate and uses a microprocessor to control the electronic pressure regulators and pressure sensors for feedback, and does not require constant bleed. This reduces the air compressor’s duty cycle, electrical cost and usage.
QBX Series Variable Pressure Regulator
- Regulation Accuracy +/-0.2% FS @ 15 psi = +/-0.03 psi (+/-0.1 psi needed, 3X better)
- Repeatability +/-0.02% FS @ 15 psi = +/-0.003 psi
- DAC 12-bit, 4.096V@4096 steps = 1 mV=0.003 psi/bit (proportional valve DAC limited)
An estimated $17,000 in annual energy savings is expected to be realized, and other optimizations to the dry air system could increase the savings even further.