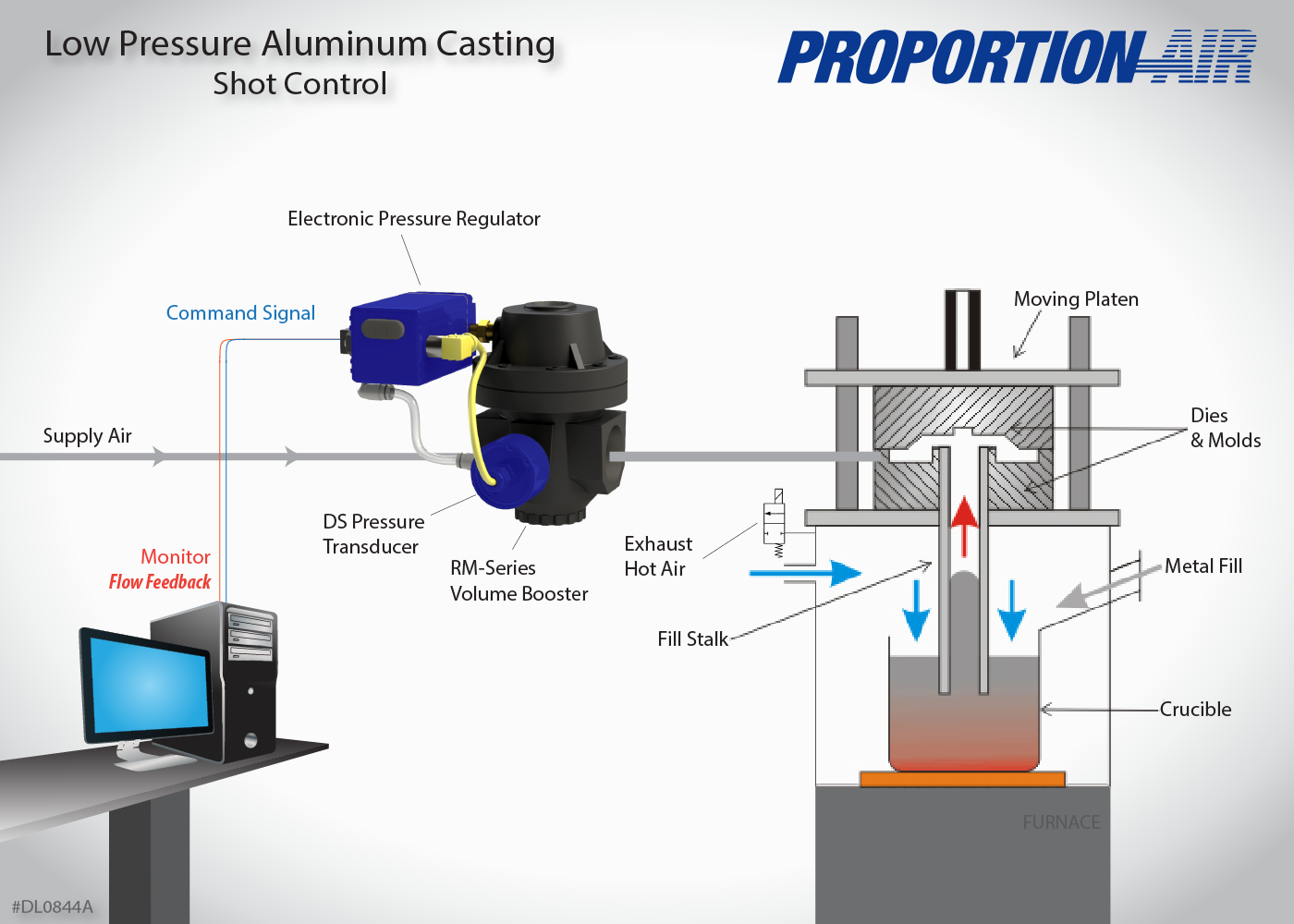
Proportion-Air Case Study
A Molten Metal Flow Control Problem
Low pressure aluminum die casting improves a cast product’s quality. High resolution is often critical for precise control of molten metal flow into the mold, and in such applications, smaller steps in pressure allow the best control of metal flow.
An OEM low pressure casting machine builder approached Proportion-Air needing to control “shot pressure” in their low pressure casting machines. They worked at pressures just above zero psig up to not greater than 15 psig, and they were looking for high resolution as well as repeatability. Their casting furnace volume was relatively large so higher flow was necessary to keep up with shot speed. At the end of the shot, the customer vented crucible pressure with a separate valve to isolate the QB2 assembly from high temperature gases of their furnace.
The Customized Regulator Solution
We specified Proportion-Air’s QB2/DSY dual close-loop electronic air pressure regulator mounted to a two-inch ported high flow air piloted volume booster. We set up the assembly so the QB2 received its supply pressure separate from the volume booster. The QB2 had supply pressure of 20 psig and the volume booster could take advantage of higher supply pressure from the factory’s compressor for increased flow rates.
The assembly was offered on a 30-day trial. It kept up with their flow requirement but they needed better performance near zero psi. We modified the volume booster to improve bottom end pressure control. The assembly performed better than they hoped and was adopted as a standard for their machines.
Metal Casting Machine
Summary
There have been many different variations of this closed loop electronic air pressure assembly over the years for a number of OEMs and end users of low pressure casting machines.
Advantages of using Proportion-Air’s dual closed loop servo control valve include:
- Achieve high flow by using a volume booster (air piloted regulator) up to four-inch ported as part of the assembly.
- Achieve high accuracy by using the QB2 dual loop electronic pressure regulator.
- Easily monitor signal of the volume booster’s pressure downstream by connecting pin 5 of the main electrical connector to a panel meter, a multimeter, or an analog input to the customer’s controller.
- Optionally add second monitor signal (if required). Often the casting furnace will begin to leak over time, and the QB2 will compensate for furnace leaks since it is a closed loop device. However, if leaks in the furnace exceed the capacity of the QB2 assembly full shot pressure will not occur. The second monitor signal can monitor leaks in the furnace and determine when they are about to exceed the flow capacity of the Proportion-Air assembly.
- Track the command signal and adjust pressure in real time as the customer’s controller modifies the command signal – no PID tuning required.
- Improve product quality and reduce scrap due to the QB2 assembly’s repeatability of ±0.02% of full scale calibration.
Only looking for a replacement product? Please use this form
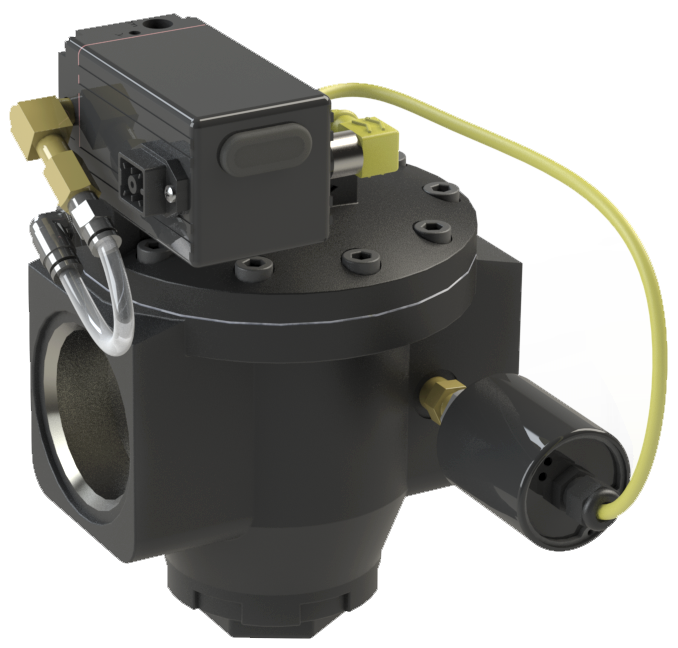