
Background
AeroParts is a company that serves the aerospace industry with the restoration of complex OEM components for aircraft. Among those critical and expensive components are the ozone converters that provide safe cabin air. AeroParts services over one half of the world’s fleet of ozone converters. Their services include testing and a proprietary process that restores up to 99% of the converter’s original performance. More than 99% of all ozone converters received are returned to service, virtually eliminating scrap events.
AeroParts has invested heavily in building an extensive exchange pool, so there is no need for their customers to stock expensive spares that could potentially sit in inventory for a year or two.
Problem
Reducing costs while maintaining the highest standards for safety and performance are critical in the aviation industry. As an FAA certified and authorized provider of refurbished aerospace components, the company is overwhelmed with demand. Turnaround on the ozone converters takes weeks and requires tedious labor that extends the refurbishing process timeline. The company needed a solution for improving their labor intensive testing processes, both to improve employee safety and promote efficiency.
An AeroParts process improvements specialist and engineer, Ashfaq Ali, noticed that the technicians involved in the testing and refurbishing work on the ozone converters were subjected to repetitive motion and straining that put them at risk for injury. The test benches require the control of air pressure and flow, which the operators would have to adjust using manual pressure regulators. These pressure regulators were located on the air supply lines, and not easily accessible. Adjustment was not only tedious, but also detrimental to their health.
The company wanted to ensure that technicians did not develop any kind of long-term health issues with their elbows or joints from having to rotate a knob countless times per day.
Solution
Impressed with the proven longevity and reliability of the Proportion-Air QB2 volume air booster assemblies, which the company had been using for over 10 years, Ali turned to Proportion-Air for dependable components for his improved test system design. Since the aviation industry requires the reading of absolute air pressure rather than gauge air pressure, it was also important that Proportion-Air offers both options.
The new system allows technicians to adjust the air pressure in the testing process by turning a ten turn potentiometer connected to the pressure regulator. This eliminates the need for rotating an awkwardly located mechanical pressure regulator knob manually, many times over the course of an eight to ten hour shift.
Ali plans to eventually take automation of the system further by incorporating a computer control system using 0-10vdc analog output signal, which will allow for remote adjustment at a computer. The Proportion-Air products are completely compatible with computer interface capabilities necessary to meet these automation goals.
Overall, Ali has been very impressed with the quality of the Proportion-Air product line and very pleased with the level of support he has received from the company.
Three Distinct Components
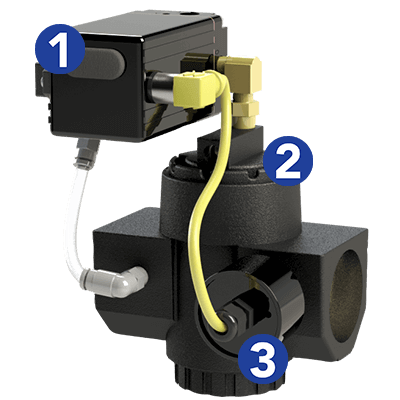
When an application requires more flow than a single unit can offer, our QB & volume booster assemblies can meet your needs.
1 – QB2X Electronic Pressure Regulator provides an air pilot signal to the dome of the air volume booster. By controlling pressure to the top of the diaphragm, we control pressure out of the volume booster.
2 – An Air Volume Booster, also known as a dome-loaded or pilot-operated pressure regulator. This can be a pressure reducing valve or a back pressure valve. We have many volume boosters available that can handle different pressures, medias and flow rates. Understanding the application is critical to specifying the best fit.
3 – A DSB or DST Pressure Transducer measures output pressure of the volume booster and provides this feedback signal to the QB2. The QB2 adjusts dome pressure (based on this feedback) to achieve the commanded pressure in the process.