It’s the middle of April, it’s finally warming up and the pneumatic lab team from Purdue Polytechnic Institute can feel the end of the school year upon them. They’ve nearly completed their entire capstone project, but a couple steps remain for Gate 5.
Building the lab
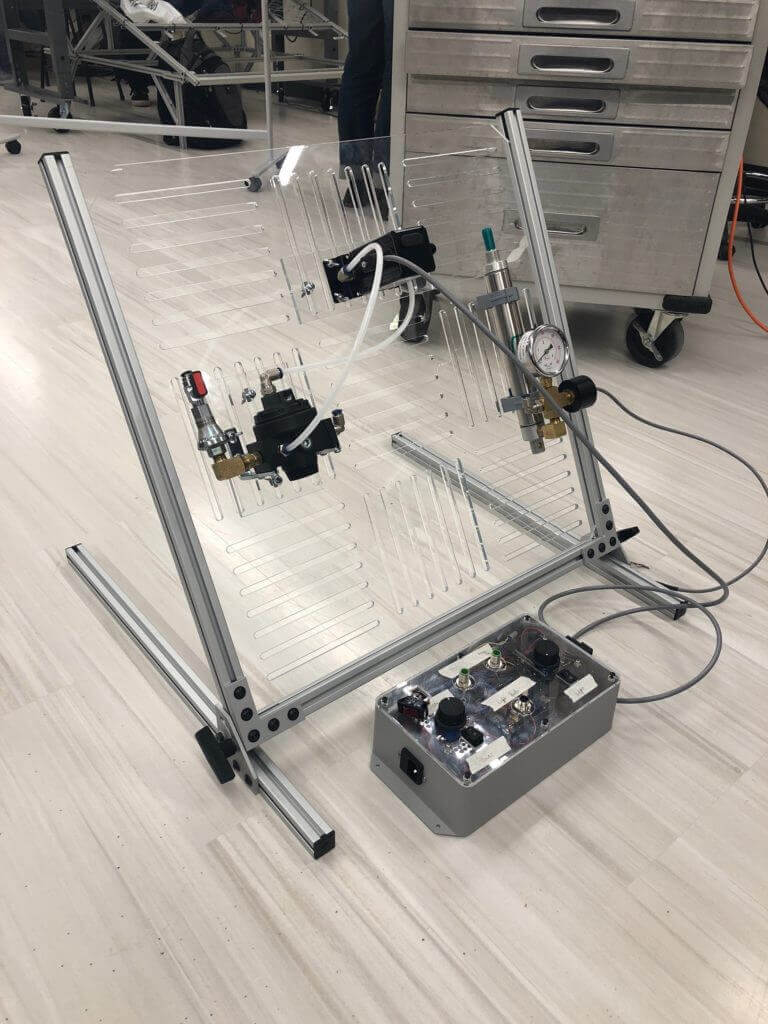
Early in the capstone, the team had several ideas for what the final lab unit might look like – Is it a self-contained box? How will all of the lab materials fit? How will all of the components interact?
With a little bit of inspiration from Proportion-Air staff, the team built the lab frame using 80/20 T-slot aluminum framing. They selected a clear acrylic backing to mount components. Grooves laser-cut into the acrylic make it easy to slide components into different locations. The frame is adjustable, so students can change the angle of the work surface.
They also designed an electrical control box that contains the usual suspects: a power supply, switches, potentiometers and a microcontroller. The students chose an Arduino as the microcontroller, writing a program for each of the labs to acquire the necessary data.
Troubleshooting
Once they assembled the frame and acrylic part of the unit, it was time to add components. One of the biggest challenges came when interfacing the QBX, one of our electro-pneumatic pressure regulators, with the turbine. The pneumatic lab team’s idea was to send the voltage generated from the turbine back to the QBX. However, because the output voltage was not directly compatible, the students created an analog circuit that converted the voltage to a usable feedback signal. The team decided to install a needle valve before the turbine to demonstrate how it all works.
This part of the project showed the team the importance of closed-loop feedback. The needle valve they installed allows them to manually adjust the flow going into the turbine. By controlling the flow, the team can safely regulate the speed of the turbine, which was turning as fast as 24,000 RPM. In an open-loop system, when the needle valve is opened, flow increases and the output voltage of the turbine also increases. However, by using closed-loop design, the QBX senses the increase in voltage and dynamically adjusts the flow to keep the voltage steady.
These challenges gave the students a lesson into the importance of testing. Everything had been assembled to plan, but putting the parts together isn’t enough – the labs have to perform as intended. While it took several weeks to get the first unit to operate correctly, once it was done, the team built the remaining two units in a couple days.
Classroom experience
After being reviewed by the team’s advisor, Dr. José Garcia, the labs were cleared for classroom experimentation. Jacob Torres, one of Garcia’s teaching assistants, is using them in MET 230. The students in the course are currently trying them and will provide feedback.
Adjustments made from the current students’ feedback are the final piece of Gate 5. Gate 6 – the last gate and finish line – is a poster presentation at the Purdue Polytechnic Institute Tech Expo on April 27. Instructors attending the expo will grade the team.
What’s next?
Three members of the team will graduate in May, while the remaining member stays in West Lafayette until December. Our final update will include the students’ plans for the future.